The importance of matching the right heat-transfer press with your dye-sublimation printer
by Lily Hunter, Product Manager for Dye-Sublimation Technology at Roland DGA
Okay, so you’ve got a dye-sublimation printer in mind, but you’re wondering what kind of heat press will complete your perfect dye-sublimation workflow? There are many options out-there and choosing the right heat press isn’t easy. Much depends on the type of products and applications that are in your business plan, and other factors, like size, type, and cost will need to be considered.
Heat presses are designed for specific applications and come in all styles, sizes and with very different price tags – presses can run from $1K to $100K. The following tips outline some of the most important points to keep-in-mind when purchasing a heat press to combine with your dye-sublimation printer.

You have to be willing to invest in a heat press – go cheap and you might end up with a glorified sandwich maker!
Make the Investment – For the Long-Term
Why invest in high-quality dye-sublimation printing technology like the Roland DG XT-640 or RT-640 that produces a high-quality product, just to compromise on a cheap heat press and shoot yourself in the foot? If you base your decision solely on price, then you may regret it in the long run. Whether you’re looking for a small-format or large-format heat press, cheaper models simply don’t offer the build quality or level of sustained heat and pressure that is required to produce professional results when transferring graphics.
Some of the cheaper clam, swing away and flatbed heat presses have flimsy heater blocks made from thin materials that heat up fast but cool down too quickly – failing to maintain an even heat. Whereas a machine with a heavy platen takes longer to heat up but maintains a regular heat and ensures that each press has the same consistency and quality of image and color. When physically comparing heat presses, trust your instincts. If a press doesn’t feel robust and well-made, then it most likely isn’t and probably won’t perform properly.
What to Look for in a Perfect Press
Does size matter?
Firstly, you’ll need to think about what your end game is, i.e., what are you producing and what do you plan to produce. Heat presses range in heat block sizes from around 6”x 8” for a light-use press, right up to oversized 44”x 64” and beyond. Right now, you’re probably considering either a desktop-sized press for apparel or product customization, or a shop-sized press that will allow you to branch out into fabrics, soft-signage and larger scale sublimation.
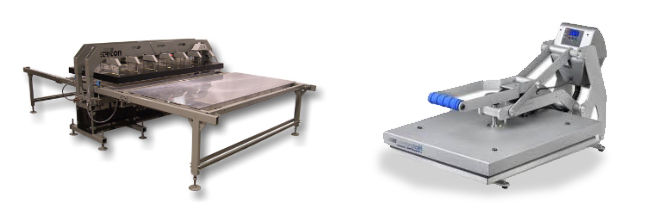
(left) large-format flatbed press from Geo-Knight – built for shop production of large fabrics, decor, soft-signage etc. (right) Hotronix clam press in desktop and benchtop models – designed to produce a range of small and large t-shirt and apparel production.
The size of heat presses are so many and varied. As a rule, it’s always better to think bigger to allow yourself the ability to expand your product range. However, if you want something strictly for simple customizations of t-shirts and apparel, a large flatbed or calender press can sometimes be counter-productive and you’ll find that a smaller swing-away or clam press for different apparel sizes is actually more efficient. You may find that a couple of these smaller sized heat presses that can be operated by multiple people might be more effective for your production model than one large-format machine.
Consistent heat
Heat presses need to be heated to about 400 degrees fahrenheit for sublimation inks to transfer from the paper to the polymer fibers. This transfer has to be smooth and even for the process to work properly and for the image transfer to be consistent from one pressing to the next. Some heat presses may look really high-tech and snazzy, but under-the-cover it may be a different story.
Another issue with cheaper heat presses is having too few heater windings (heater coils) in heater blocks or heater windings that are too sparsely placed. This causes cold spots and inconsistent transfer. The more windings a press has, the quicker it will heat up and regain any heat loss between jobs.
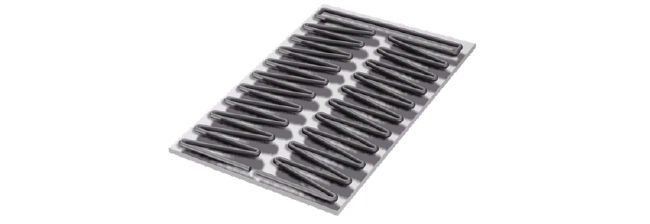
An internal view of what heater windings from a heat block should look like – this example shows the double heater coil SuperCoil-Microwinding™ technology from Geo Knight.
Considering that you can’t see the heater windings in a heater block, you’ll have to do your homework and make sure to ask dealers or manufacturers the right questions and do your due diligence in comparing machines for these unseen features. Also look for differences in the wattage of heater windings that also effects heat consistency. Higher wattage is always better.
Consistent pressure
Maintaining consistent pressure during the heat transfer process is extremely important. A quality heat press has a heavy platen that generates enough weighted-pressure for a clean heat transfer without any cold spots. Cheaper models lack the necessary platen weight and struggle to maintain transfer consistency.
Heat and pressure testing with heat strips
If possible, it’s recommended that you test out a heat press for heat and pressure consistency before purchasing. Even a quality press may have warped platens, cracked rubber pads, ineffective heater windings or other issues that can cause cold spots. You can purchase a test kit from Stahls’ or other heat press manufacturers to check pressure and temperature results. These kits contain special paper strips that when placed in the heat press, heated and then pressed, can indicate uneven pressure and inaccurate heat application.
Pressure gauge
To make production easier while ensuring image uniformity, it’s also preferable to choose a heat press model with a pressure gauge. Pressure gauges are extremely useful for showing users exactly how much pressure is being added to each pressing and in doing so, adding much better color and image consistency to the finished product.
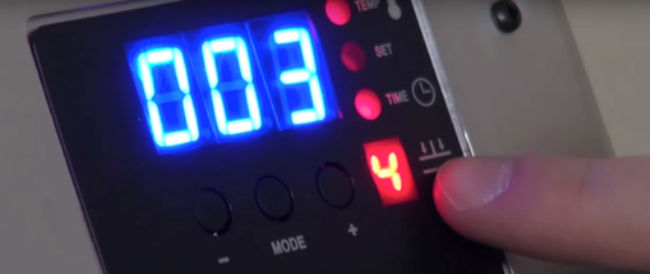
Example of a timer and pressure gauge features with a “no. 4” setting to maintain pressure consistency throughout all pressings.
Timer
Timing is very important during the heat transfer process. If a heat press is operated beyond the recommended sublimation time, the inks will continue to gas out to the point of fading. Therefore, longer press time doesn’t necessarily mean better images and each dye will reach a certain plateau of color intensity before fading out. Consistent timing produces better results.
Having a timer on your heat press that times each pressing and alerts users to when it's completed is a majorly useful feature on both digital and analog models for ensuring consistency. Some of the newer heat press models also have an automated open feature at the end of their timed cycle in which the platen pops up when the pressing is complete. If you’re running a busy shop, then having these kind of unattended press features can save you a lot of hassle.
What’s my Type?
When considering a heat press, there are a number of distinct types that work with different types of media. The following devices enable effective transfer onto different sizes and substrate types:
Clam Press
The compact and convenient t-shirt ‘clam’ press is the most common heat press machine and is used to transfer onto apparel and small-coated items such as tiles and metal signs. It is also used to produce small fabric color proofs before full production printing. A great machine for people looking to customize t-shirts, sweatshirts and basic apparel. Very effective, but limited in its product scope.
Clam press by Maxx.
Swing Away
More hi-tech than the clam press, the swing away is designed to handle different media thicknesses. It has a more advanced set-up and operation that always lays the platen flat against the media being imprinted. Most swing away presses will work with media that’s at least 1-inch thick, allowing users to heat transfer onto more items, such as plaques and photo frames. The swing-away action of the machine also prevents “knuckle burns” and other problems associated with clam presses.
Swing away heat press by Hotronix.
Calender Press
Unlike the other heat presses illustrated in this post, calender presses don’t have heat blocks. Instead, they use oil or electrically heated drums to heat transfer from a printed roll of paper onto polyester fabric – the roll of paper is attached calendar pressto the press and fed through with the fabric.
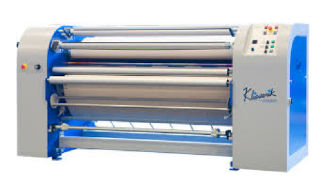
Large-format, oil drum calender press by Klieverik (above, right). Klieverik press with feed table (below, left) – ideal for feeding individual pieces.
Calender heat presses are ideal for users who want to specialize in cut/sew apparel, décor, and soft-signage. They cannot be used, however, to press rigid substrates. Prices vary a great deal and much of the cost is based on whether it’s electric or oil based and on the size of the drum – a bigger drum means a higher cost. However, a bigger drum also means greater production and faster output. Unlike smaller heat presses, calender presses require a 240V electrical outlet with a double throw (2 pole) set-up.
Calender heat presses are available in the following types:
Electric
This is considered to be more of an entry-level calender press that’s lower in cost but can still achieve professional results. Unlike the oil drum version, it’s the air in the electrical drum that’s heated, which enables it to heat up quicker and cool down faster. Something that can be an advantage if you’re running a small but efficient dye-sublimation business.
Oil Drum
Associated with professional dye-sublimation production, the oil drum version is a more expensive calendar press that needs an air compressor to run it. Available in mid-to-high volume production models, they range from shop-sized to industrial-sized presses. The oil in their drums takes longer to heat up than the air in their electrical counterparts, but they maintain heat far better over long periods of time and ensure much better heat-pressing consistency.
Flatbed Press
Flatbed presses typically have a rigid tabletop surface that supports transfers onto solid objects such as sheet metal, wood, ceramic tiles, floor mats, carpet tiles and small pre-cut fabric pieces. They are also some of the most effective machines for printing “all-over” t-shirts and apparel customization. Flatbed presses will also need a 240V electrical outlet with a double throw (2 pole) set-up.
GeoKnight Maxi-Press Air (pneumatic) Heat Press.
Flatbed presses are available in the following types:
Pneumatic
Pneumatic presses are more expensive than manual ones. Users will also need an air compressor to run them. However, having a pneumatic press makes the job a lot more automatic and hands-free, enabling users to set-up and press jobs in superfast speeds and at the touch-of-a-button. Users can set-up and walk away from the machine, rather than having to be involved in the whole pressing process.
Manual
Some users prefer the traditional flatbed heat presses that require a bit more muscle and physical control over the actual pressing operation. Despite them not having the automated features of a pneumatic model, most of the recommended manual flatbed models provide pressure, timing and self-loading features to make imprinting a semi-manual operation.
3D Vacuum Heat Press (Oven Press)
A press with an air-forced vacuum operation that wraps transfer designs around smart phone covers, ceramic plates, frames, and other irregular shaped items. They are available from Policrom in desktop and shop-sized models and require special transfer film, plus a specific fixture for sublimating each item. The ideal machine if you want to customize a range of blanks.
Small vacuum heat press from Policrom who sell transfer film and offer consultation to ensure proper fixture design.
Baseball Cap and Mug Presses
If you’re looking to add designs to a lot of baseball caps or a lot of mugs, then there are specialty presses available for both. Designed to do a single task really well, they are the perfect heat press for those users who know what they want to customize and need a specific machine to do it.
Hotronix cap heat press
When you find the right heat press to combine with your dye-sublimation printer, it’s like a match made in heaven. Just be forewarned that they are not inexpensive machines, so before making a commitment, you need to be very certain what makes the most sense for your business. Our advice is to take your time, ask questions of the dealer or manufacturer and look very closely at the warranty and support available.
- If you’re looking to get into dye-sublimation printing, see our new, high-volume Texart XT-640 printer or simply brilliant RT-640 printer, or request a free sample today.